Conventional PET Processing
PET bottles and jars exhibit superior transparency, gloss and strength and as a result have been replacing many other materials for the packaging of beverages, foodstuffs, pharmaceuticals, cleaning products, personal care products and chemicals.
PET containers are produced in two steps, firstly by injection molding of test-tube shaped PET preforms from PET granules raw material and secondly by stretch blow molding these preforms into bottles or jars.
There are two distinct processes (types of machines) that are commonly used to produce PET bottles and jars.
Two-stage process: The bottles are produced on machines that implement step 2 by taking ready preforms, heating them and stretch blow molding them into bottles. Two-stage machines are normally used for high production outputs of beverage bottles, using PET preforms with standard neck sizes, which are readily available in the market. About 80% of the PET containers produced globally are made on two-stage, re-heat stretch-blowing machines.
Conventional Single-stage process: The bottles are produced on machines that implement BOTH steps 1 and 2 by using PET raw material to mold preforms and then directly stretch-blow-molding these preforms into the finished bottles or jars. Single-stage machines are well suited to medium production rates as well as for containers with non-standard necks, for which preforms would not be readily available in the market. About 20% of the PET bottles and jars produced globally are made with single-stage machines. Such machines typically have three or four stations (injection, {conditioning,} stretch-blowing and container ejection) with a rotary indexing table for transferring the preforms between stations. There are separate clamping units for opening and closing the injection molds (vertical clamp) and the blow molds (horizontal clamp).
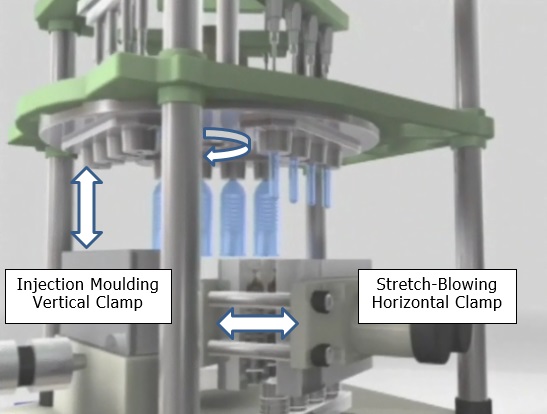
Single stage vs Two stage Injection Stretch Blow Molding Comparison:
Conventional Single stage process has the following advantages over Two Stage Process:
- Lower electricity consumption. The molded preforms do not have to be completely cooled after injection molding and then re-heated for stretch blowing.
- Lower resources requirements. No need for packing, storing and transporting preforms.
- Suitable for all containers irrespective of neck design and weight. There is no restriction to only the preforms available on the market.
- Superior container clarity and gloss, as there is no preform surface deterioration due to storage and transport.
- Flexibility to produce a very wide variety of container sizes, shapes and neck diameters on the same machine.
Two Stage process has the following advantages over Single Stage:
- Much higher production outputs are possible.
The CYPET Process
The CYPET Process is an innovative single stage process, set apart from conventional single-stage technologies. It utilizes a single clamping unit for opening and closing both the injection and the blow molds.
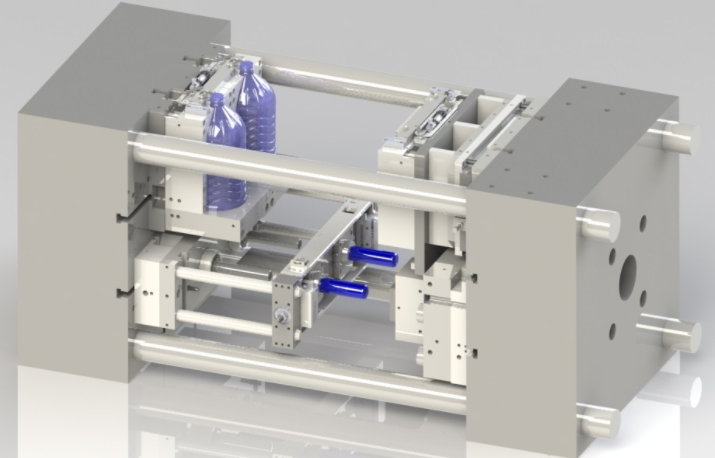
As a result, instead of using a specially designed machine, the process utilizes the clamping unit and injection unit of an injection molding machine base, converting it into a single-stage machine by integrating it with a stretch-blowing unit, a set of molds and a control system. The stretch-blowing unit carries out the functions of transferring the preforms from the injection to the blow molds, blowing them into containers and removing the finished containers. A CYPET machine can also be used as an injection molding machine, to mold preforms, caps and any other plastic article whose injection mold can fit inside the machine.
The following video shows how the CYPET Injection Stretch Blow Molding process works:
.
Please visit our YouTube channel to see CYPET machines in action producing a whole range of containers.
CYPET Benefits
CYPET systems retain all the advantages of conventional single stage systems, while offering important additional benefits:
- Lower Electricity Consumption.
- Lower investment cost for equivalent output.
- Ability to mold very large containers – allowing PET containers to expand into new markets.
- Ability to integrate handles as one piece with blown container. This lowers production costs, improves ergonomics and makes recycling easier. PET containers can now replace HDPE containers with handles.
- Higher production flexibility – allowing operation in multiple markets using just one machine both for blow molded parts as well as injection molded parts.
- All-electric production – especially suitable for medical, pharmaceutical or food contact applications.