

The CYPET Process
The CYPET Process is an innovative single stage process, set apart from conventional single-stage technologies. It utilizes a single clamping unit for opening and closing both the injection and the blow molds.
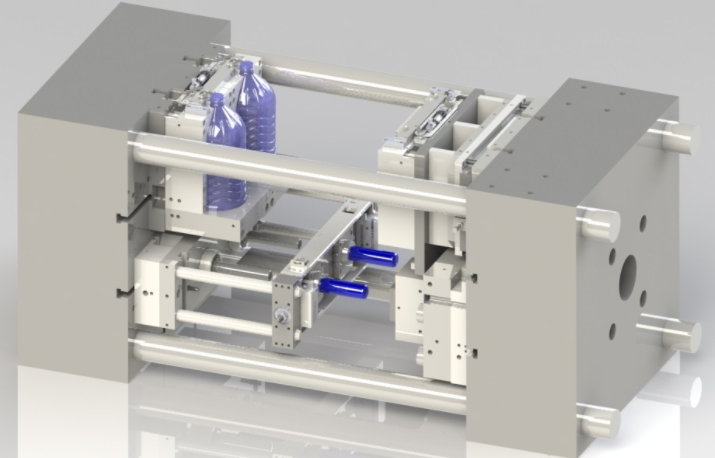
As a result, instead of using a specially designed machine, the process utilizes the clamping unit and injection unit of an injection molding machine base, converting it into a single-stage machine by integrating it with a stretch-blowing unit, a set of molds and a control system. The stretch-blowing unit carries out the functions of transferring the preforms from the injection to the blow molds, blowing them into containers and removing the finished containers. A CYPET machine can also be used as an injection molding machine, to mold preforms, caps and any other plastic article whose injection mold can fit inside the machine.
The following video shows how the CYPET Injection Stretch Blow Molding process works:
.
Please visit our YouTube channel to see CYPET machines in action producing a whole range of containers.
CYPET Benefits
CYPET systems retain all the advantages of conventional single stage systems, while offering important additional benefits:
- Lower Electricity Consumption.
- Lower investment cost for equivalent output.
- Ability to mold very large containers – allowing PET containers to expand into new markets.
- Ability to integrate handles as one piece with blown container. This lowers production costs, improves ergonomics and makes recycling easier. PET containers can now replace HDPE containers with handles.
- Higher production flexibility – allowing operation in multiple markets using just one machine both for blow molded parts as well as injection molded parts.
- All-electric production – especially suitable for medical, pharmaceutical or food contact applications.